For businesses that need walk-in coolers or freezers, choosing the right flooring can mean the difference between success and failure. The right flooring can impact long-term maintenance costs and the quality of the items stored in the walk-in. It's not a decision to take lightly. In fact, there's a list of factors to consider when choosing walk-in flooring.
Floor Basics -- Insulated Floors vs. "Floorless"
Not every walk-in comes with a floor. If temperature control is not a concern, adding sealers between the walls and floor may be enough, provided the walk-in rests on a concrete floor that sits on the ground. Do not expect the walk-in to effectively cool products if it has more than occasional foot traffic.
Insulated floors are a better option. Without proper insulation, cold air escapes, and warm air creeps in, causing inconsistent temperatures, higher humidity, and possible product loss. Even with insulated flooring, it isn't one size fits all. There are other factors to consider when selecting insulated flooring for a walk-in.
Things To Consider When It Comes To Walk-in Flooring
The EPA requires all walk-in freezers to have insulated flooring with a minimum R-28 rating. However, the agency does not have the same standards for walk-in coolers. Selecting the right flooring depends on the intended use. Will there be a lot of traffic in and out of the cooler? What will be stored in the cooler? Having the answers to these questions makes it easier to find the best insulated flooring solution.
Location
Condensation damages flooring. Over time, the water damage from condensation compromises a building's integrity. To protect against potential water damage, coolers should be placed on a concrete slab that sits on the ground. The insulated flooring then sits on the slab. Concrete limits heat transfer and reduces wear and tear on walk-in units. In hot and humid environments, walk-in units should rest on a concrete slab.
Moisture
Insulated floors are required if walk-in coolers are over a crawl space, basement, or above the first floor of a building. Because warm air circulates under the unit, insulated flooring reduces the condensation that can form between the unit and the underlying structure. Condensation buildup means wet floors and wet floors equal accidents. According to the Bureau of Labor Statistics, close to 25% of on-the-job accidents are the result of slips, trips, and falls.
Access
How will products be moved in and out of the cooler? Will ramps be needed for carts and rolling racks? If ramps are needed, will they obstruct a walkway or thoroughfare? Sometimes, the floor can be recessed to allow true walk-in access. Deciding on cooler access before installation makes for a smoother implementation.
Traffic
Walk-in coolers are used for everything from flowers to kegs. They may be opened and closed anywhere from one to one hundred times a day. Product may be hand-carried or transported using pallet jacks. The amount and kind of traffic should determine the type of insulated flooring to use.
Flooring Types
Insulated flooring can be configured to support loads from light foot traffic to heavy, stationary loads. Choosing the right flooring for a given application means considering the location, traffic, and access requirements.
The Thermo-Kool Difference
Thermo-Kool offers walk-in coolers and freezers in custom sizes. Floors can be smooth or treadplate aluminum, stainless steel, or galvanized steel; however, the galvanized steel must be covered with tile or concrete to meet NSF standards. We also provide heavy-duty support floor structures for installations requiring support for up to 12,000 lbs per square foot of stationary load.
Wondering if your walk-in cooler or freezer is built to stand the test of time? Click below to download our free checklist to get started.
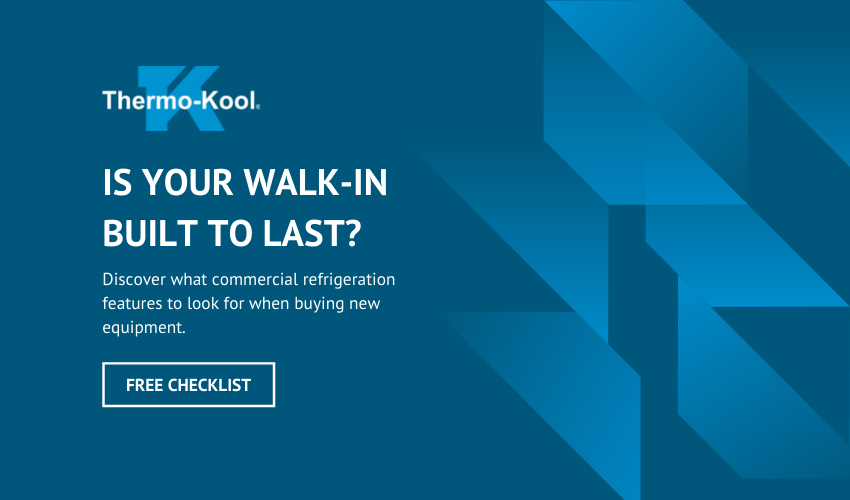